Operation Guide
Side Thrust
This term refers to the maximum force that can be safely applied in a lateral direction. If this force exceeds the specified maximum value, the traverse unit may slip on the shaft.
Pitch
Pitch denotes the linear movement of the traverse unit per one full rotation of the shaft. The pitch reaches its maximum value at a dial setting of 10. For precise adjustments, shift the pointer lever along the dial. For optimal accuracy and performance, it is recommended to operate the traverse unit at a setting above 1 on the dial.
Maximum Pitch
The maximum pitch is the linear movement achieved per one full rotation of the shaft, typically set at a dial setting of 10.
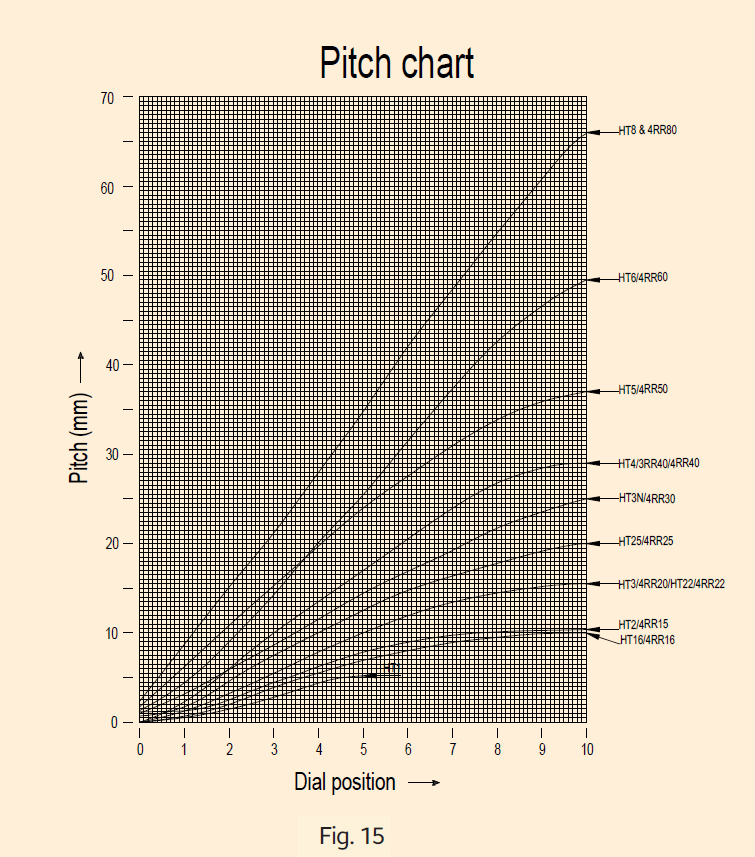
Adjusting the pitch
To change the pitch, press the pointer lever down and move it along the dial.
Linear speed
Depends on both the shaft speed and the pitch setting.
Shaft speed
Calculated based on the maximum pitch of the traverse unit and the required linear speed.
Recommended shaft speed
